Yield Monitor Calibration: Planning For Quality Data Collection
Sep 09, 2021
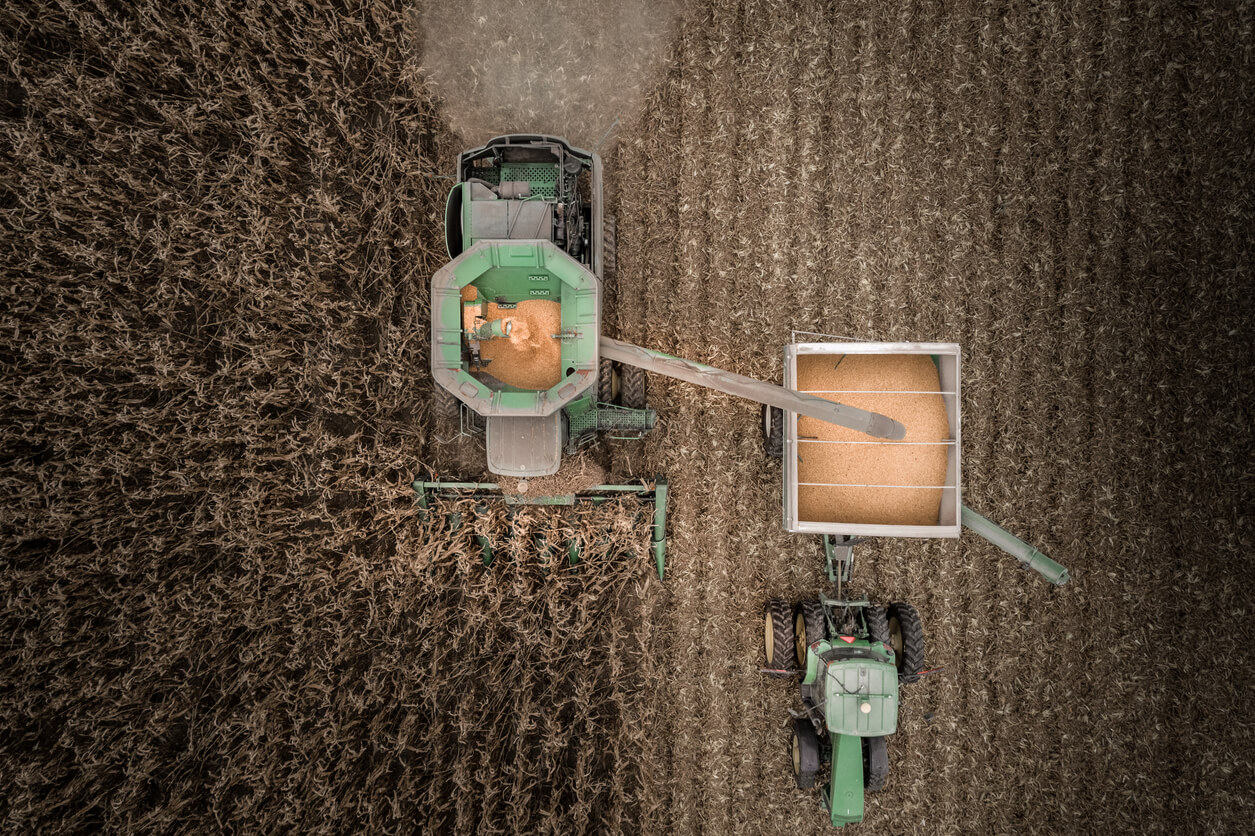
Some of you may be in the heat of harvest while others are gearing up to begin shortly. Here are some considerations to think through as you plan to collect quality yield data that you can use for future management decisions. Even if you don’t think you will need the data today or you plan to use it for decision making soon, I still urge you to do your best in collecting quality data and archiving it in AccuField®.
If you wait to collect good data until you are ready to use it, we will be starting from scratch and have years ahead of us to aggregate the foundation of farm datasets worthy of decision-making. If you begin today implementing good data collection strategies and store the data with your trusted advisor in AccuField®, you will be well on your way to reaping immediate benefits when the day comes, and you want to use yield data for management decisions.
Yield monitors are a great source of detailed data that have a lot more to offer than a grain weight ticket or gin ticket. Accurate yield data collected over time allows a grower to begin making data-driven management decisions and assess field performance at a scale otherwise unattainable. It is important that yield monitors be calibrated for accurate data collection, but they also must be setup properly so there are no data overlaps or skips (Figure 1.) within the data from inaccurate GPS settings. To accomplish this, you will want to make sure the combine header or picker heads are setup correctly in the display, the horizontal and vertical GPS offsets are correct in the display, and a recent calibration has been performed on the TCM (terrain compensation module).
The settings and accurate calibration are even more important when multiple machines are harvesting simultaneously within a field to ensure that the data is synchronized and that one or multiple machines are not creating a skewed data set (Figure 2.). Calibration of look-ahead or flow delay settings are very important as well. The material being harvested can spend several seconds traveling through a machine before being read by a sensor. Figure 3 illustrates gaps in data due to erroneous look-ahead or flow delay settings. This setting tells the GPS when and where to geo-tag yield measurements taken by sensors.
Take Home Message
When yield monitors are correctly calibrated, it is very easy to assess whole field yield based off the data collected. Accuracy errors typically range from 7-10% before calibration and higher if the monitor is taken straight off the shelf and used in a machine. The data collected can aid in identifying factors that are limiting yield. With accurate data, management zones can be produced and used for input strategies, soil sampling, in-season applications of nitrogen, plant growth regulators, defoliants, or even nematicides.
Calibration of newer harvesters is becoming increasingly more convenient and easier. Manufacturers are adding onboard technology to the degree that self-calibration is a reality today. We are working toward the day when in-field weigh wagons or scales will no longer be needed; however, our ag technology specialists are equipped to handle all of your calibration needs. Whether you need in-field or over the phone solutions, we’ve got you covered. Reach out to your local GreenPoint Ag or member cooperative today and let us help you with a data collection game plan that will make a positive impact on your operation.
Figure 1:
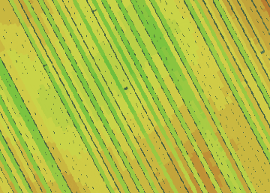
Figure 2:
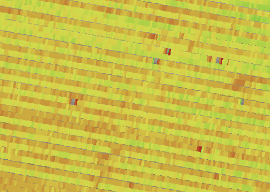
Figure 3:
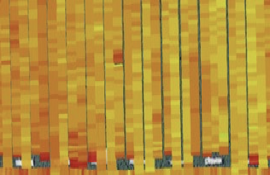
This article was written by Daniel Mullenix, Senior Manager of Ag Technologies at GreenPoint Ag. You can reach him at daniel.mullenix@greenpointag.com.
If you wait to collect good data until you are ready to use it, we will be starting from scratch and have years ahead of us to aggregate the foundation of farm datasets worthy of decision-making. If you begin today implementing good data collection strategies and store the data with your trusted advisor in AccuField®, you will be well on your way to reaping immediate benefits when the day comes, and you want to use yield data for management decisions.
Yield monitors are a great source of detailed data that have a lot more to offer than a grain weight ticket or gin ticket. Accurate yield data collected over time allows a grower to begin making data-driven management decisions and assess field performance at a scale otherwise unattainable. It is important that yield monitors be calibrated for accurate data collection, but they also must be setup properly so there are no data overlaps or skips (Figure 1.) within the data from inaccurate GPS settings. To accomplish this, you will want to make sure the combine header or picker heads are setup correctly in the display, the horizontal and vertical GPS offsets are correct in the display, and a recent calibration has been performed on the TCM (terrain compensation module).
The settings and accurate calibration are even more important when multiple machines are harvesting simultaneously within a field to ensure that the data is synchronized and that one or multiple machines are not creating a skewed data set (Figure 2.). Calibration of look-ahead or flow delay settings are very important as well. The material being harvested can spend several seconds traveling through a machine before being read by a sensor. Figure 3 illustrates gaps in data due to erroneous look-ahead or flow delay settings. This setting tells the GPS when and where to geo-tag yield measurements taken by sensors.
Take Home Message
When yield monitors are correctly calibrated, it is very easy to assess whole field yield based off the data collected. Accuracy errors typically range from 7-10% before calibration and higher if the monitor is taken straight off the shelf and used in a machine. The data collected can aid in identifying factors that are limiting yield. With accurate data, management zones can be produced and used for input strategies, soil sampling, in-season applications of nitrogen, plant growth regulators, defoliants, or even nematicides.
Calibration of newer harvesters is becoming increasingly more convenient and easier. Manufacturers are adding onboard technology to the degree that self-calibration is a reality today. We are working toward the day when in-field weigh wagons or scales will no longer be needed; however, our ag technology specialists are equipped to handle all of your calibration needs. Whether you need in-field or over the phone solutions, we’ve got you covered. Reach out to your local GreenPoint Ag or member cooperative today and let us help you with a data collection game plan that will make a positive impact on your operation.
Figure 1:
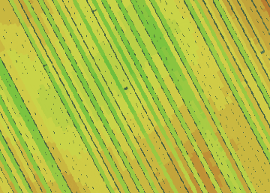
Figure 2:
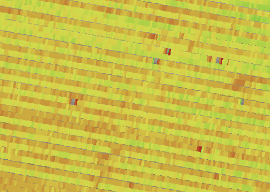
Figure 3:
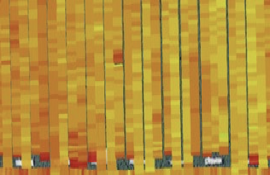
This article was written by Daniel Mullenix, Senior Manager of Ag Technologies at GreenPoint Ag. You can reach him at daniel.mullenix@greenpointag.com.